Design of a thermal control system for an IC test-in-tray handler
Author(s)
Pfahnl, Andreas Carl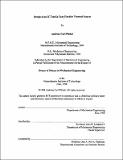
DownloadFull printable version (70.88Mb)
Advisor
John H. Lienhard, V.
Terms of use
Metadata
Show full item recordAbstract
This work reports the design of a fundamentally new semiconductor integrated circuit (IC) test handler thermal system, and its implementation in the development of a new commercially-sold product. The test handler is a manufacturing machine that automates the mechanical handling of IC devices for testing at any temperature in the range of-60°C to 160°C to a tolerance down to ± 1°C. A complete formulation and documentation for the design of the handler thermal system has been developed based on specific functional requirements and design objectives. The inability to deterministically design handler thermal systems and resolve thermal-related issues hinders the development of future semiconductor products, such as the upcoming RAMBUS or Synclink chips (high speed memory). To commercialize such new products, IC manufacturers must always wait for the development and production of higher performing test equipment which must meet ever-more stringent and higher performance requirements. Implementation of the design approach has resulted in novel heat-transfer-related technologies, enabling test-equipment manufacturers to provide high-performance test solutions. An extremely-compact turbulent air-flow thermal-conditioning chamber has been developed to depress or elevate (-60°C to 160°C) the temperature of ambient devices at rates over 10,000 uph, using a 32-device test tray. Novel heat-transfer enhancing rib features have been incorporated into a new thin small-outline package (TSOP-II) handler test tray to help maximize throughput. Experimental wind tunnel tests have demonstrated about 100% faster thermal-response times of this tray than conventional TSOP process trays. Finally, a novel heat-conduction plate is developed that provides a compact means to control the temperature of the handler test interface. The plate relies on having a high thermal conductivity to uniformly heat or cool the electrical test contactors fastened to the plate - an approach much different than conventional methods. Initial testing has shown the site-to-site temperature variation of a 32-contactor plate to be ± 20C at 100 oC. The compactness of the thermal plate allows electrical transmission path lengths from the contact pins of the test head to leads of the device under test (DUT) to be reduced to about 2.54 cm (1.0").
Description
Thesis (Sc.D.)--Massachusetts Institute of Technology, Dept. of Mechanical Engineering, 1998. Includes bibliographical references (p. 423-430).
Date issued
1998Department
Massachusetts Institute of Technology. Department of Mechanical EngineeringPublisher
Massachusetts Institute of Technology
Keywords
Mechanical Engineering