Optimization of the glass fiber forming process for single-tip and small-number-tip positions
Author(s)
Ansbergs, Christa R., 1976-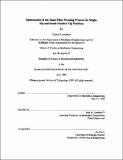
DownloadFull printable version (15.08Mb)
Advisor
John H. Lienhard, V.
Terms of use
Metadata
Show full item recordAbstract
The design of fiberglass manufacturing setups has evolved largely by trial and error. Efforts are now in place to achieve a better understanding of the fiber forming process. To facilitate this research, a smaller and simpler version of the full-scale fiber forming process is being used. This system has vastly different geometry and produces a small number of fibers. Work in this project has concerned optimization of the small-scale process to more closely match the behavior to production line fiberglass forming positions, such that results of experiments on the smaller system are applicable to the full scale system. Efforts were also put into simplification of the system, such that process variables can more easily be isolated for further study. The primary effort of this project was put into controlling glass head pressure. On the full-scale system constant glass depth is maintained and the glass weight controls the flow rate of glass through the fiber forming tips. On the small system flow rate is controlled by a combination of changing glass weight and added air pressure. The pressure control system developed in this project uses glass resistance to measure glass depth and outputs a signal to a solenoid valve to add the appropriate amount of air pressure above the glass. The glass resistance measuring system had to be calibrated for a range of temperatures. Resistance data was collected while mass flow of glass was monitored. From the mass flow glass depth was calculated to an accuracy of 3%. When set to simulate the full-scale fiberglass forming operation the pressure control valve can control pressure to within 4.5% of 5.5 kPa required pressure. A new fiber winding system was designed and implemented. This system assures even distribution of fibers along the axis of a winder drum, speed control to within 1%, and limited vibration transmission to the fibers while they are in the forming and cooling regions. The pressure control and winder control systems were incorporated into the same LabView interface to assure ease of use. From the interface an operator can set winder speed and total head pressure and monitor the control of both to assure that the system is behaving appropriately.
Description
Thesis (S.M. and S.B.)--Massachusetts Institute of Technology, Dept. of Mechanical Engineering, 1999. Includes bibliographical references (p. 93).
Date issued
1999Department
Massachusetts Institute of Technology. Department of Mechanical EngineeringPublisher
Massachusetts Institute of Technology
Keywords
Mechanical Engineering