A wireless robotic manipulator for semiconductor manufacturing equipment
Author(s)
Scrivens, Jevin E. (Jevin Eugene)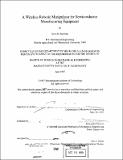
DownloadFull printable version (47.95Mb)
Advisor
Alexander Slocum.
Terms of use
Metadata
Show full item recordAbstract
Silicon wafer processing is an extremely refined and sensitive operation. Processing often takes place in clean rooms filtered to better than class 1. However even under these precautions, particle contamination still causes failures in the microchips produced in these environments. One source of these contaminants is the production equipment itself. Particularly, the wire carriers connecting the robots can shed micro particles which are deposited onto the wafers in process. The wires within these carriers also possess a considerable failure rate which causes machine down time and contamination of the environment due to the repair operation. These combined factors illustrate the need to minimize the use of wire carriers. The solution to these problems is the concept of the wireless robot. The wireless robot uses inductive power transfer and optical communication to operate the end effector of the robot. This takes advantage of the fact that for many types of production equipment, the robots only need to execute more complex motions at discrete locations. In its overall operation, the robot is positioned in front of an operation station where a pair electromagnetic coils would be aligned. The primary coil would be fixed to the station and the secondary coil would be attached to the robotic manipulator. The primary coil would be charged by a high frequency AC supply, and the property of electromagnetic induction would cause a similar voltage to be produced in the secondary coil. This voltage would then be supplied to the electronics of the manipulator as a power source. Robot control would be achieved through the use of optical transfer rather than a hardwired voltage transfer. This technique is similar to well known processes used in fiber optics, however in this process the transfer median is an air gap rather than a fiber optic cable. This design calls for the use of only one way transmission where the transmitters are on the base and the receptors are on the robot. Two way transmission for feedback is possible and available for future use. This design also lends itself to a variety of other applications including factory automation robots and other environments in which operation is required in discrete locations or sensitive environments.
Description
Thesis (S.M.)--Massachusetts Institute of Technology, Dept. of Mechanical Engineering, 1997.
Date issued
1997Department
Massachusetts Institute of Technology. Department of Mechanical EngineeringPublisher
Massachusetts Institute of Technology
Keywords
Mechanical Engineering