Three dimensional printing with fine metal powders
Author(s)
Baker, Peter R. (Peter Ross)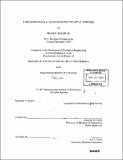
DownloadFull printable version (32.04Mb)
Alternative title
3D printing with fine metal powders
Other Contributors
Massachusetts Institute of Technology. Dept. of Mechanical Engineering.
Advisor
Emanuel M. Sachs.
Terms of use
Metadata
Show full item recordAbstract
In the area of direct metal part manufacture, the 3DPTM process has several inherent advantages over traditional machining and P/M technologies: hard tooling is not required to manufacture parts, geometries may be created which can not be made by conventional processes, and the composition of parts may be controlled locally on a 100 gm scale. The surface finish of 3DPTM parts will be a key factor in the determination of what parts are candidates for direct manufacture via the 3DPTM process. Powder size is the limiting factor in the determination of the surface finish of 3DPTM parts. On the micro scale, it determines the roughness due to particle arrangement, and on the macro scale it determines the thinnest layers from which parts may by built. The 3DPTM process has been adapted to a fine metal powder (ten micron particle diameter) material system. Powder spreading, ink-jet technology, and the effect of print parameters on printing with fine metal powders have been examined. Powder spreading experiments were conducted to examine the limits of layer thickness and packing density. 420 ss, S-7 tool steel, and 316L ss powderbed beds were generated in fifty micron layers. Packing densities of 55%, 59% and 59% respectively were obtained for the three powders. Line printing experiments were conducted with both continuous jet (CJ) and drop on demand (DOD) printheads to examine the relationship between droplet frequency, droplet spacing and the quality of printed lines. Lines were printed at droplet frequencies ranging from 100 Hz to 40 kHz and with droplet spacings from ten to fifty microns. Low print frequencies and small droplet spacings result in the highest quality lines. A droplet spacing of thirty microns and a droplet frequency of 667 Hz was chosen for the printing of 3-D parts with a Hewlett- Packard DOD printhead. 3-D part geometries were generated using fifty micron layers of ten micron 420 ss powder. These parts demonstrated the improvement in surface finish achieved with fine metal powders and the capability to create parts from fields identified as promising for the direct fabrication of metal parts via the 3DPTM process.
Description
Thesis (S.M.)--Massachusetts Institute of Technology, Dept. of Mechanical Engineering, 1997. Includes bibliographical references (leaf 97).
Date issued
1997Department
Massachusetts Institute of Technology. Department of Mechanical EngineeringPublisher
Massachusetts Institute of Technology
Keywords
Mechanical Engineering.