A flexible assembly system for low volume and high diversity production
Author(s)
Schwenke, Richard Clemens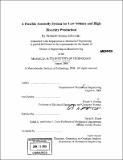
DownloadFull printable version (64.25Mb)
Other Contributors
Massachusetts Institute of Technology. Dept. of Mechanical Engineering.
Advisor
Duane S. Boning.
Terms of use
Metadata
Show full item recordAbstract
This thesis project seeks to optimize floor layouts for semiconductor equipment assembly operations. The assembly of semiconductor equipment is characterized by low volume and high product diversity and complexity. Demand for semiconductor equipment is highly periodic and often shifts rapidly from one type of semiconductor equipment to the other. Thus, the goal is to develop an assembly system that easily handles high part counts per assembly and facilitates material management, but at the same time allows reacting to changes in demand quickly and efficiently. Lead time and floor space usage are further metrics that are considered. Capturing the current state of the floor layout in a 3D drawing software and documenting important aspects of current operations is the first step towards achieving those goals. Current assembly operations consist of the build of subassemblies in dedicated cells and the final assembly of machines in dedicated build lines. That is, each type of product is assembled in a specific area and the required inventory is stored within these areas. In order to increase production flexibility, reduce inventory levels, and to lower floor space usage, a new assembly system is developed. This system features consolidated inventory for both the build of subassemblies and final assembly. It is proposed that technicians pull parts for subassemblies by driving with a cart and attached foam cut-outs as part trays through an inventory aisle. This aisle accommodates inventory for all subassemblies, which is currently stored within approximately 20 cells spread over the production floor. (cont.) Subsequently, technicians drive these carts to generic workbenches and start assembly. Using generic, standardized workbenches rather than dedicated workbenches boosts flexibility and efficiency. Parts for the final assembly would be kitted for each machine by material handlers on movable racks. This allows building any type of machine in any area of the production floor. A block system is proposed to decouple assembly of different machines and to enable easy management of assembly operations. A floor layout based on these ideas is developed. Finally, a pilot proposal is developed to serve as a stepping stone towards full scale implementation and this proposal is in part physically implemented.
Description
Thesis (M. Eng.)--Massachusetts Institute of Technology, Dept. of Mechanical Engineering, June 2009. "August 2008." Page 120 blank. Includes bibliographical references (p. 119).
Date issued
2009Department
Massachusetts Institute of Technology. Department of Mechanical EngineeringPublisher
Massachusetts Institute of Technology
Keywords
Mechanical Engineering.