Acoustic and thermal packaging of small gas turbines for portable power
Author(s)
Tanaka, Shinji, S.M. Massachusetts Institute of Technology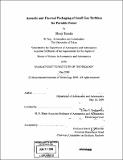
DownloadFull printable version (32.37Mb)
Other Contributors
Massachusetts Institute of Technology. Dept. of Aeronautics and Astronautics.
Advisor
Zoltán S. Spakovszky.
Terms of use
Metadata
Show full item recordAbstract
To meet the increasing demand for advanced portable power units, for example for use in personal electronics and robotics, a number of studies have focused on portable small gas turbines. This research is concerned with gas turbine generator units in the 1 kW range. The compact and small-scale architecture of the portable gas turbine engine poses major challenges in the acoustic treatment that is required to attenuate the broadband and tonal noise of the high-speed turbomachinery. The challenge in the thermal management is the relatively large required cooling mass flow and the short flow mixing length, constrained by package size considerations. The objective is to conceive a proof-of-concept engine package with exhaust temperatures of 60 °C and a noise signature below 50 dBA at a distance of 7 m. Various liner materials and configurations were investigated in an anechoic chamber using a modular silencer test rig. Acoustic liners based on porous fiber material were developed for both cold intake and hot exhaust gas silencers to reduce the broadband noise. The source noise simulations combined with the measured silencer noise reduction show noise levels below 50 dBA in all directions. A parametric silencer configuration study was carried out to determine the trade-off between liner volume, surface area, and noise reduction. The liner material was demonstrated to withstand hot gas conditions at 700 °C. (cont.) A mixer/ejector based cooling scheme was proposed and experimentally investigated using vortex generator rings and multi-walled ejectors to enhance the mixing. Although the augmentations achieved a satisfactory mass flow ratio of 16.8:1, hot spots still exist at the exit of the relatively long mixer duct due to the high area-ratio of the ejector configuration. It was concluded that implementation of the scheme into the package is not practical. To overcome this mixing challenge, an alternative cooling scheme was conceived. An inverted dilution liner mixes hot core gas flowing radially through a perforated cylinder with cold fan air. The mixing length is reduced due to jet induced streamwise vortices. The performance of the device was investigated using three-dimensional computational fluid dynamics simulations, which demonstrated improved mixing and uniform, low temperatures of less than 70 °C at the mixer exit. Noise reduction and flow mixing guidelines are established together with a concept package configuration, generally applicable to small scale gas turbine devices.
Description
Thesis (S.M.)--Massachusetts Institute of Technology, Dept. of Aeronautics and Astronautics, 2009. Includes bibliographical references (p. 201-203).
Date issued
2009Department
Massachusetts Institute of Technology. Department of Aeronautics and AstronauticsPublisher
Massachusetts Institute of Technology
Keywords
Aeronautics and Astronautics.