Lean strategies for future body shop development and operation in the automotive industry by Iker Marcaide.
Author(s)
Marcaide, Iker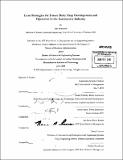
DownloadFull printable version (5.917Mb)
Other Contributors
Leaders for Global Operations Program.
Advisor
Daniel Whitney and Steven Spear.
Terms of use
Metadata
Show full item recordAbstract
There are several body shops which are similar by size of workforce, level of utilization and product complexity but which differ considerably by investment required, shop size, uptime, inventory levels and quality accomplished. The purpose of this thesis is to explain why those differences exist. The methods used to understand differences were direct observation, first hand working experience on the line and participation in workshops, analysis of internal and external bibliography, and interviews to line workers, supervisors and managers within different functions. Differences are observed and described in the design and operation of the shops. A "Lean" body shop, named in such a way given their reduced use of resources to accomplish better results, follow an integrated design process where product and process are tightly integrated, maintain similar product architectures across generations enhancing standardization and modularity, similar shop architectures across plants, close relationships with suppliers, elimination of complexity in manufacturing processes, flexible conveyance processes and the use of proven technologies. In addition, a lean body shop's operation works as a coherent and integrated set of practices under three systems: The Social System: Engagement and development of workforce that acts as enabler; The Technical System: Tools to reduce waste and increase quality; The Problem Solving & Continues Improvement System: An ever learning and improving organization where problems are visualized, solved and countermeasures implemented and shared. Finally, this thesis provides insights into the change management processes associated with the transformation into lean body shops, from establishing a sense of urgency and guiding coalition to empowering broad based action employee action and anchoring new approaches in the culture, and performs a case analysis on a successful lean transformation: NUMMI.
Description
Thesis (M.B.A.)--Massachusetts Institute of Technology, Sloan School of Management; and, (S.M.)--Massachusetts Institute of Technology, Engineering Systems Division; in conjunction with the Leaders for Global Operations Program at MIT, 2010. Cataloged from PDF version of thesis. Includes bibliographical references (p. 56-59).
Date issued
2010Department
Leaders for Global Operations Program at MIT; Massachusetts Institute of Technology. Engineering Systems Division; Sloan School of ManagementPublisher
Massachusetts Institute of Technology
Keywords
Sloan School of Management., Engineering Systems Division., Leaders for Global Operations Program.