A process for separation by semi-continuous counter-current crystallization
Author(s)
Aumock, Nathan M. (Nathan Micheal)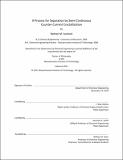
DownloadFull printable version (2.114Mb)
Other Contributors
Massachusetts Institute of Technology. Dept. of Chemical Engineering.
Advisor
Kenneth A. Smith.
Terms of use
Metadata
Show full item recordAbstract
A process is proposed to perform separations via crystallization by using multiple tanks and constraining crystal growth to solid surfaces. Multiple tanks allow multiple recrystallizations to improve product purity and to ensure high recovery of the component of interest. Crystal growth on solid surfaces avoids multi-phase flow handling which can cause operational difficulties. A model is developed for this process for solid solution forming systems which is also applied to batch crystallization for comparison. The solid product from the process is found to provide enhanced purity (1-2% increase) at yields approaching the batch yield when a large number of tanks are used; the ratio of incorporation rate constants (?) is significantly less than one; and the surface equilibrium constant (K) is less than order one. The liquid effluent from the process is also a viable product when ?>1 and K is close to or greater than one. The use of a sweep stream entering at a tank up-stream of the feed tank was determined to be undesirable due to diminished yield. Batch experiments performed to validate the proposed model with asparagine as the component of interest and aspartic acid as the impurity in water were found to be inconclusive. Fitting of parameter values to the liquid phase was not successful due to crystal growth on surfaces other than the designated seed. The parameters ? and K fitted to solid phase data were found to be 0.1-3 and 0.4-0.6 respectively which are favorable parameters for use of the semi-continuous process with the solid taken as the product. The presence of crystals on multiple surfaces in the liquid phase indicates that constraint of crystallization to a specific surface was not achieved. The impurity distribution in the solid layer did not match the model prediction throughout the crystal. Non-uniform initial growth behavior or uneven dissolution of the crystal during analysis could cause the observed behavior. Further experiments should be conducted that in-crease the ratio of product to accumulation in the liquid phase and employ solid sampling methods that give more consistent results.
Description
Thesis (Ph. D.)--Massachusetts Institute of Technology, Dept. of Chemical Engineering, 2011. This electronic version was submitted by the student author. The certified thesis is available in the Institute Archives and Special Collections. Cataloged from student submitted PDF version of thesis. Includes bibliographical references (p. 223-230).
Date issued
2011Department
Massachusetts Institute of Technology. Department of Chemical EngineeringPublisher
Massachusetts Institute of Technology
Keywords
Chemical Engineering.