Development of a representative volume element of lithium-ion batteries for thermo-mechanical integrity
Author(s)
Hill, Richard Lee, Sr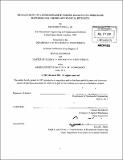
DownloadFull printable version (14.54Mb)
Other Contributors
Massachusetts Institute of Technology. Dept. of Mechanical Engineering.
Advisor
Tomasz Wierzbicki.
Terms of use
Metadata
Show full item recordAbstract
The importance of Lithium-ion batteries continues to grow with the introduction of more electronic devices, electric cars, and energy storage. Yet the optimization approach taken by the manufacturers and system designers is one of test and build, an approach that nearly every other industry has long abandoned. A computational model is required to reduce the expensive build-test cycle and allow safer, cheaper batteries to be built. The path to building this computational model will involve many different processes and one of those processes dictates the homogenizing of the interior of the battery casing by treating the interior as a homogenized Representative Volume Element. This study explains this process and outlines a procedure for the development of this particular model for both cylindrical and prismatic / pouch cells. Over twenty different mechanical tests were performed on fully-discharged cylindrical and pouched / prismatic lithium-ion batteries, in casings and without casings under multiple loading conditions. These included lateral indentation by a rod, axial compression, through-thickness compression, in-plane unconfined compression, in-plane confined compression, hemispherical punch indentation and three-point bending. Extensive testing on the battery cell and jelly roll of 18650 lithium ion cylindrical cell, combined with the use of analytical solutions to estimate material properties of the cell, yielded the development of a finite element model. It was found that the suitably calibrated model of high density compressible foam provided a very good prediction of the crash behavior of cylindrical battery cell subjected to high intensity lateral and axial loads. For the prismatic / pouch cell, the measured load-displacement data allowed calculation of the individual compression stress-strain curves for the separator, the active anode and cathode materials. The average stress-volumetric strain relation was derived from averaging the properties of individual layers as well as from direct measurement on the bare cell. This information was then used as an input to the FE model of the cell. The model was composed of shell elements representing the Al and Cu foil and solid elements for the active material with a binder lumped together with the separator. Very good correlation was obtained between LS-Dyna numerical simulation and test results for the through-thickness compression, punch indentation and confined compression. Closed form solutions were also derived for the latter three problems which helped explain the underlying physics and identified important groups of parameters. It was also demonstrated that a thin Mylar pouch enclosure provided considerable reinforcement and in some cases changed the deformation and failure mechanism. This paper reports on the results generated for the Li-ion Battery Consortium at MIT.
Description
Thesis (Nav. E. and S.M.)--Massachusetts Institute of Technology, Dept. of Mechanical Engineering, 2011. Cataloged from PDF version of thesis. Includes bibliographical references (p. 67-69).
Date issued
2011Department
Massachusetts Institute of Technology. Department of Mechanical EngineeringPublisher
Massachusetts Institute of Technology
Keywords
Mechanical Engineering.