A capital equipment capacity planning methodology for aerospace parts manufacturing in a high-mix, low volume environment
Author(s)
Reveley, Matthew A. (Matthew Aaron)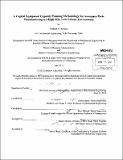
DownloadFull printable version (9.609Mb)
Alternative title
capacity planning methodology for aerospace parts manufacturing in a high-mix, low volume environment
Other Contributors
Leaders for Global Operations Program.
Advisor
David Hardt and Roy Welsch.
Terms of use
Metadata
Show full item recordAbstract
A static capacity planning model was developed and tested following a four-phased framework. This model was developed for the purposes of capital planning for capacity requirements at a large aerospace parts manufacturing plant. Implications for capacity planning of the nature of the aerospace industry, as well as the company and plant being studied are discussed, as well as the current state of capacity planning. In phase I of model development, an appropriate modeling solution is selected. In phase II, information is collected from the user base as to the desired user experience and functionality of the model, as well as the parameters that should be considered in it. Phase III involves assessment of the parameters' impact on capacity, and identification of appropriate data sources to feed the model. Additionally, phase III recommends changes to current data structures in order to optimize the balance of model accuracy with minimal incremental resource allocation. In phase IV, the mathematical model is explained, and the user interface is developed. With a working model, the results are validated with the shop floor, identifying gaps in data sources previously unobservable. Following model development and validation, the model is applied to a subset of the shop, and used to develop recommendations for addressing predicted future capacity constraints. Application of the model reveals a blind spot in current heuristics-based planning, where high development loads can lead to immediate capacity constraints, but effects of the experience curve can actually cause this constraint to disappear on its own, without the need for excess equipment purchases. Finally, extensions of the research and lessons learned are discussed, suggesting future project work within the plant studied, as well as elsewhere in the company and in other companies or plants.
Description
Thesis (M.B.A.)--Massachusetts Institute of Technology, Sloan School of Management; and, (S.M.)--Massachusetts Institute of Technology, Dept. of Mechanical Engineering; in conjunction with the Leaders for Global Operations Program at MIT, 2012. Page 99 blank. Cataloged from PDF version of thesis. Includes bibliographical references (p. 97-98).
Date issued
2012Department
Leaders for Global Operations Program at MIT; Massachusetts Institute of Technology. Department of Mechanical Engineering; Sloan School of ManagementPublisher
Massachusetts Institute of Technology
Keywords
Sloan School of Management., Mechanical Engineering., Leaders for Global Operations Program.