Directional impedance of geared transmissions
Author(s)
Wang, Albert Duan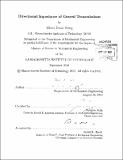
DownloadFull printable version (3.332Mb)
Other Contributors
Massachusetts Institute of Technology. Dept. of Mechanical Engineering.
Advisor
Sangbae Kim.
Terms of use
Metadata
Show full item recordAbstract
The purpose of this research is to develop a design tool for geared actuation systems that experience bidirectional exchange of energy with the environment. Despite the asymmetry of efficiency depending on the direction of power transfer in geared systems, typical dynamic models consider a fixed transmission efficiency for all conditions which can result in significant error depending on specific gear selection and the number of stages. This error can cause issues especially in dynamic legged robots and haptic devices when accurate force control is desired. In this paper we present directional impedance, a characteristic of geared transmissions in which the amount of power loss through the transmission differs according to the direction of power flow. Typical robots use electric motors with high gear reduction which introduces larger impedance when power flows from the output back to the motor than when the power flows from motor to output. To investigate the dependence on power flow direction, friction loss from gear teeth sliding in the gear mesh is modeled by a single gear tooth contact model and dynamic models are presented for each power transfer direction. Combinations of 0.5 mod gears were tested in experiment over a range of sizes between 16 and 120 teeth to characterize the directional effects over multiple gear selections. The experiments confirmed that for a set of differently sized gears, power loss is greater when the larger gear drives the smaller one than in the reverse case, and the asymmetry was up to 17% in the 16 and 120 tooth gear set. With a multiple stage gearbox, the difference in loss is further amplified. These findings show that directional loss in gears is a non-negligible effect and must be considered in both dynamic modeling and gear selection of robotic actuators. The gear loss model enables the modeling of motor and gearbox as a single package which can then be optimized for desired performance parameters such as peak torque, torque per mass, and mechanical impedance.
Description
Thesis (S.M.)--Massachusetts Institute of Technology, Dept. of Mechanical Engineering, 2012. Cataloged from PDF version of thesis. Includes bibliographical references (p. 39).
Date issued
2012Department
Massachusetts Institute of Technology. Department of Mechanical EngineeringPublisher
Massachusetts Institute of Technology
Keywords
Mechanical Engineering.