Ink jet printing of PZT thin films for MEMS
Author(s)
Bathurst, Stephen, 1980-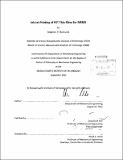
DownloadFull printable version (17.45Mb)
Alternative title
Ink jet printing of lead zirconate titanate thin films for microelectromechanical systems
Other Contributors
Massachusetts Institute of Technology. Dept. of Mechanical Engineering.
Advisor
Sang Gook Kim.
Terms of use
Metadata
Show full item recordAbstract
Of the readily available piezoelectric engineering materials perovskite phase lead zirconate titanate (PZT) has the strongest mechanical to electrical coupling. PZT based devices have the potential to have the highest performance. Due to the strong piezoelectric response and low operating voltage, many groups have worked to integrate thin film PZT into a wide range of microelectromechanical systems (MEMS) devices including: actuators, energy harvesters, resonators, pressure sensors, pumps, nano-positioning stages, and MEMS switches. However, processing of thin film PZT is not readily compatible with existing MEMS fabrication processes and significant design constraints exist when integrating thin film PZT. In recent years drop-on-demand (DOD) printing has been studied as a robust, flexible, and inexpensive method of material deposition for MEMS. Direct printing enables the designer to deposit a film based on a digital pattern file only eliminating the need for photolithography and subsequent etching steps in the manufacturing process flow. There is a significant cost savings due to a reduction in the material consumption during manufacturing and in chemical waste produced. The result is a manufacturing process that is cleaner and cheaper than other common deposition techniques. The most compelling benefit of direct printing of PZT is that it provides a freedom of geometry that eliminates many of the design constraints currently associated with PZT MEMS. Since high quality thin films can be achieved with deposition control that is not possible with spin coating, novel functionalities can be incorporated into PZT MEMS. Specifically, PZT printing is able to deposit material over and around large out-of-plane features. In addition, the thickness of thin film PZT can vary deterministically across a device or across a wafer. A new manufacturing method for the deposition of PZT thin films based on ink jet printing has been developed and used to fabricate a piezoelectric micromachined ultrasonic transducer. A solvent system and processes parameters were established that enable the deposition of high quality PZT thin films. Substrate temperature and drop spacing for uniform deposition were determined and both multilayer and single layer PZT films were successfully deposited. Alignment within 10[mu]m and a resolution limit of 30[mu]m were demonstrated. The performance of a printed PZT based ultrasonic transducer was fit to established models to determine piezoelectric coupling and dielectric properties. The piezoelectric coupling coefficient, d₃₁, for printed PZT was between -75pC/N and -95pC/N. Impedance data at 1kHz provided the relative permittivity (750-890) and the dielectric loss tangent (2.4%-2.8%). The final printing process enabled the first digital deposition of thin film PZT and the printed PZT based pMUT confirmed the properties of the film are within the range required for a high performance piezoelectric MEMS devices.
Description
Thesis (Ph. D.)--Massachusetts Institute of Technology, Dept. of Mechanical Engineering, 2012. Cataloged from PDF version of thesis. Includes bibliographical references (p. 108-113).
Date issued
2012Department
Massachusetts Institute of Technology. Department of Mechanical EngineeringPublisher
Massachusetts Institute of Technology
Keywords
Mechanical Engineering.