Development of an air-cooled, loop-type heat pipe with multiple condensers
Author(s)
Kariya, H. Arthur (Harumichi Arthur)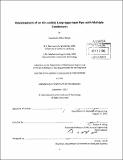
DownloadFull printable version (31.70Mb)
Other Contributors
Massachusetts Institute of Technology. Dept. of Mechanical Engineering.
Advisor
Evelyn N. Wang.
Terms of use
Metadata
Show full item recordAbstract
Thermal management challenges are prevalent in various applications ranging from consumer electronics to high performance computing systems. Heat pipes are capillary-pumped devices that take advantage of the latent heat of vaporization of a working fluid to achieve low thermal resistance (~0.1 °C/W), and have been of particular interest to address these thermal management needs for cooling solutions such as air-cooled heat sinks. This thesis reports the design, fabrication, and characterization of a novel loop-type heat pipe with multiple condensers for a high performance air-cooled heat sink. While multiple-condenser heat pipes have been developed in the past, this heat pipe layout is the first to ensure equal operation of the individual condensers. The layout incorporates wicks in both evaporator and condenser; the wick in the evaporator supplies the capillary pressure to drive the circulation and the wick in the condenser uses capillary pressure to separate the vapor and liquid phases for controlled condensation. Additionally, methods of liquid and vapor pressure control are developed to modulate the capillary pressure in the condenser. The heat pipe was first evaluated using an analytical model to determine the required thermophysical properties and geometries of the capillary wicks in the evaporator and condenser. The model results were subsequently used to obtain a detailed evaporator design that is compatible with the multiple-condenser layout. The evaporator was fabricated with a multi-step metal sintering process, characterized, and integrated into both single-condenser and six-condenser prototypes. The prototypes successfully operated in a wide range of angles, with automatic heat pipe startup and with a heat pipe thermal resistance as low as 0.0065 °C/W with equal condenser performance. The air-cooled, six-condenser prototype demonstrated removal of 500 W from a heat source at 75 °C. The heat pipe cycle developed in this study enables the use of multiple condensers in a loop-type heat pipe to achieve a large surface area with little thermal resistance for heat sink applications.
Description
Thesis (Ph. D.)--Massachusetts Institute of Technology, Dept. of Mechanical Engineering, 2012. Cataloged from PDF version of thesis. Includes bibliographical references (p. 169-172).
Date issued
2012Department
Massachusetts Institute of Technology. Department of Mechanical EngineeringPublisher
Massachusetts Institute of Technology
Keywords
Mechanical Engineering.