Recycling production designs : the value of coordination and flexibility in aluminum recycling operations
Author(s)
Brommer, Tracey H. (Tracey Helenius)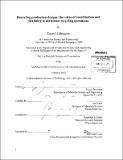
DownloadFull printable version (33.55Mb)
Alternative title
Value of coordination and flexibility in aluminum recycling operations
Other Contributors
Massachusetts Institute of Technology. Department of Materials Science and Engineering.
Advisor
Joel Clark and Randolph Kirchain.
Terms of use
Metadata
Show full item recordAbstract
The growing motivation for aluminum recycling has prompted interest in recycling alternative and more challenging secondary materials. The nature of these alternative secondary materials necessitates the development of an intermediate recycling facility that can reprocess the secondary materials into a liquid product. Two downstream aluminum remelters will incorporate the liquid products into their aluminum alloy production schedules. Energy and environmental benefits result from delivering the products as liquid but coordination challenges persist because of the energy cost to maintain the liquid. Further coordination challenges result from the necessity to establish a long term recycling production plan in the presence of long term downstream aluminum remelter production uncertainty and inherent variation in the daily order schedule of the downstream aluminum remelters. In this context a fundamental question arises, considering the metallurgical complexities of dross reprocessing, what is the value of operating a coordinated set of by-product reprocessing plants and remelting cast houses? A methodology is presented to calculate the optimal recycling center production parameters including 1) the number of recycled products, 2) the volume of recycled products, 3) allocation of recycled materials across recycled products, 4) allocation of recycled products across finished alloys, 4) the level of flexibility for the recycling center to operate. The methods implemented include, 1) an optimization model to describe the long term operations of the recycling center, 2) an uncertainty simulation tool, 3) a simulation optimization method, 4) a dynamic simulation tool with four embedded daily production optimization models of varying degrees of flexibility. This methodology is used to quantify the performance of several recycling center production designs of varying levels of coordination and flexibility. This analysis allowed the identification of the optimal recycling center production design based on maximizing liquid recycled product incorporation and minimizing cast sows. The long term production optimization model was used to evaluate the theoretical viability of the proposed two stage scrap and aluminum dross reprocessing operation including the impact of reducing coordination on model performance. Reducing the coordination between the recycling center and downstream remelters by reducing the number of recycled products from ten to five resulted in only 1.3% less secondary material incorporated into downstream production. The dynamic simulation tool was used to evaluate the performance of the calculated recycling center production plan when resolved on a daily timeframe for varying levels of operational flexibility. The dynamic simulation revealed the optimal performance corresponded to the fixed recipe with flexible production daily optimization model formulation. Calculating recycled product characteristics using the proposed simulation optimization method increased profitability in cases of uncertain downstream remelter production and expensive aluminum dross and post-consumed secondary materials.
Description
Thesis (Ph. D.)--Massachusetts Institute of Technology, Dept. of Materials Science and Engineering, 2013. Cataloged from PDF version of thesis. Includes bibliographical references (p. 212-219).
Date issued
2013Department
Massachusetts Institute of Technology. Department of Materials Science and EngineeringPublisher
Massachusetts Institute of Technology
Keywords
Materials Science and Engineering.