Issue resolution at a large aerospace manufacturer
Author(s)
Clarke, Sarah (Sarah Kathleen)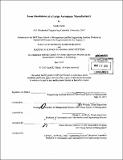
DownloadFull printable version (4.847Mb)
Other Contributors
Leaders for Global Operations Program.
Advisor
Roy Welsch and Olivier L. de Weck.
Terms of use
Metadata
Show full item recordAbstract
UTC Aerospace Systems has a wide variety of problem solving tools driven by their Achieving Competitive Excellence (ACE) program. One tool that is frequently used to resolve and capture customer escapes is the 8D methodology. It is an eight-step process designed to identify, correct, and eliminate recurring problems and is useful in providing a feedback mechanism between the customers and suppliers. Its goal is to establish a permanent corrective action and focuses on the origin of the problem by determining its root causes. The objective of the project is to fully understand the cost benefit of implementing the 8D methodology. The initial investigation of the 8D process uncovered that some defects recorded using the 8D tool are omitted in metrics reporting, leading to poor issue resolution and limited feedback between customers and suppliers. Because the tool requires additional steps that were not required in previous problem solving techniques at UTC Aerospace Systems, it is both more cost and time intensive. To avoid wasteful spending, it is therefore important that the tool be applied only when necessary. A study was performed to identify situations when the 8D tool is used improperly. Two situations were identified: (1) when an 8D investigation is performed unnecessarily and (2) when the 8D investigation is not performed in a situation when it should be. In the first situation, the unnecessary implementation of the 8D tool results in wasted effort within the organization. In the second situation, the missed opportunity to implement the tool has the potential to allow future occurrences of the same defect that may have otherwise been avoided. Preventing a defect from occurring in the future is often achieved by redesigning a part to eliminate a systemic issue. It is therefore important to use the 8D tool in order to identify systemic issues more quickly and thereby reduce future repair costs. The costs associated with these two situations are further quantified in the project.
Description
Thesis (S.M.)--Massachusetts Institute of Technology, Engineering Systems Division; and, (M.B.A.)--Massachusetts Institute of Technology, Sloan School of Management; in conjunction with the Leaders for Global Operations Program at MIT, 2013. Cataloged from PDF version of thesis. Includes bibliographical references (p. 39-40).
Date issued
2013Department
Leaders for Global Operations Program at MIT; Massachusetts Institute of Technology. Engineering Systems Division; Sloan School of ManagementPublisher
Massachusetts Institute of Technology
Keywords
Engineering Systems Division., Sloan School of Management., Leaders for Global Operations Program.