Design and control of a self-sensing piezoelectric reticle assist device
Author(s)
Amin-Shahidi, Darya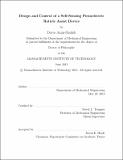
DownloadFull printable version (16.55Mb)
Other Contributors
Massachusetts Institute of Technology. Department of Mechanical Engineering.
Advisor
David L. Trumper.
Terms of use
Metadata
Show full item recordAbstract
This thesis presents the design and control techniques of a device for managing the inertial loads on photoreticle of lithography scanners. Reticle slip, resulting from large inertial loads, is a factor limiting the throughput and accuracy of the lithography scanners. Our reticle-assist device completely eliminates reticle slip by carrying 96% of the inertial loads. The primary contributions of this thesis include the design and implementation of a practical high-force density reticle assist device, the development of a novel charge-controlled power amplifier with DC hysteresis compensation, and the development of a sensorless control method. A lithography scanner exposes a wafer by sweeping a slit of light passing through a reticle. The scanner controls the motion of the reticle and the wafer. The reticle-stage moves the photoreticle. To avoid deforming the reticle, it is held using a vacuum clamp. Each line scan consists of acceleration at the ends of the line and a constant-speed motion in the middle of the line, where exposure occurs. If the reticle's inertial force approaches or exceeds the clamp's limit, nanometer-level pre-sliding slip or sliding slip will occur. The assist device carries the inertial load by exerting a feedforward force on the reticle's edge. The device retracts back during the sensitive exposure interval to avoid disturbing the reticle. The reticle is at the heart of the scanner, where disturbances directly affect the printing accuracy. Our reticle assist device consists of an approach mechanism and a piezoelectric stack actuator. The approach mechanism positions the actuator 1-m from the reticle edge. The actuator, with 15-[mu]m range, extends to push on the reticle. We have developed control techniques to enable high-precision high-bandwidth force compensation without using any sensors. We have also developed a novel charge-controlled amplifier with a more robust feedback circuit and a method for hysteresis compensation at DC. These technologies were key to achieving high-bandwidth high-precision sensorless force control. When tested with a trapezoidal force profile with 6400 N/s rate and 60 N peak force, the device canceled 96% of the inertial force.
Description
Thesis (Ph. D.)--Massachusetts Institute of Technology, Dept. of Mechanical Engineering, 2013. This electronic version was submitted by the student author. The certified thesis is available in the Institute Archives and Special Collections. Cataloged from student-submitted PDF version of thesis. Includes bibliographical references (p. 233-239).
Date issued
2013Department
Massachusetts Institute of Technology. Department of Mechanical EngineeringPublisher
Massachusetts Institute of Technology
Keywords
Mechanical Engineering.