Assembling 3D MEMS structures by folding, aligning and latching 2D patterned films
Author(s)
Shaar, Nader S. (Nader Salah)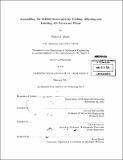
DownloadFull printable version (15.75Mb)
Alternative title
Assembling three-dimensional micro-electro-mechanical systems structures by folding, aligning and latching two-dimensional patterned films
Other Contributors
Massachusetts Institute of Technology. Department of Mechanical Engineering.
Advisor
George Barbastathis and Carol Livermore.
Terms of use
Metadata
Show full item recordAbstract
The techniques used in the fabrication of micro-electro-mechanical systems (MEMS) were adopted from the integrated circuits (IC) industry and are mostly limited to patterning thin films on a flat substrate. As a consequence, micro-machined devices mostly comprise sets of flat two-dimensional (2D) membranes with etched patterns and undercuts that enable them to serve their intended functions. However, many mechanical, optical and biological applications, such as corner-cube retro reflectors, micro-scale magnetometers, 3D microfluidic systems and 3D photonic crystals, require three-dimensional (3D) geometries for their functionality. In addition, 3D circuits have also emerged as a way of improving connectivity and reducing power dissipation in electronic chips. However, the creation of fully 3D structures via conventional MEMS fabrication techniques typically requires processes that have low throughput, limited control over the final geometry, and higher costs. A promising alternative to 3D microfabrication that addresses these challenges while requiring minimal investment in a new infrastructure is to use the existing technologies to pattern in 2D, and then assemble the patterned segments into 3D structures. Demonstrated methods to achieve that objective have been limited in scope, requiring manual assembly or with limited applicability to specific architectures. This thesis presents a coherent modular system for folding, aligning and latching 2D-patterned precursors into prescribed 3D structures. The system presented here comprises flexure hinges to enable relative motion among the 2D precursors, a cascaded alignment system to provide progressively better alignment among precursors as they approach their final positions, and systems of reversible latches to retain the assembly in its final configuration while, optionally, permitting disassembly and reassembly of the structure. In particular, two types of systems are considered. First, the design, fabrication and testing of polymer structures with metal hinges, cascaded alignment features and integrated latching mechanisms are presented for perpendicular assembly of structures. Second, an alternative latching technique using controlled melting of photoresist polymer adhesive pads is analyzed and tested for the parallel assembly of structures. The structures discussed in this thesis consist of SU-8 polymer segments patterned on silicon wafers and linked with an underlying thin gold pattern that defines the hinges. The elasto-plastic bending of the hinges is analyzed and simulated to predict the trajectory and angular position of the membranes during folding. The design of cascaded alignment features, consisting of triangular protrusions and corresponding rhombic holes, is discussed. A kinematic model of the alignment mechanism is presented to demonstrate the effectiveness of the cascading aspect of the design to achieve a large range of angular correction and high alignment accuracy at the same time. The design of micro snap-fit latches that work in conjunction with the alignment system is also presented, and quasi-static simulations of the elastic bending of latches is used to evaluate their strength. Experimental measurements were conducted to characterize the behavior of the gold hinges during bending, demonstrating good agreement with models. The integrated folding-alignment-latching system was demonstrated by assembling corner-cube structures. The alignment process was found to be accurate to within 1 from measurements of the final assembled position of the corner cube structure. The system was also shown to support fabricating reconfigurable devices by demonstrating the ability to unlatch and re-latch segments. The latching and unlatching forces were measured to be 9.7 [mu]N and 12.3 [mu]N respectively.
Description
Thesis: Ph. D., Massachusetts Institute of Technology, Department of Mechanical Engineering, 2014. Cataloged from PDF version of thesis. Includes bibliographical references (pages 116-121).
Date issued
2014Department
Massachusetts Institute of Technology. Department of Mechanical EngineeringPublisher
Massachusetts Institute of Technology
Keywords
Mechanical Engineering.