Improving sales and operations planning in an engineer-to-order environment
Author(s)
Christogiannis, Andreas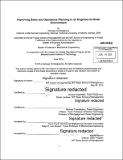
DownloadFull printable version (15.83Mb)
Other Contributors
Leaders for Global Operations Program.
Advisor
Donald Rosenfield and Michael Triantafyllou.
Terms of use
Metadata
Show full item recordAbstract
A pragmatic approach is taken at analyzing and improving Sales and Operations Planning in a project based, engineer-to-order product line. Variability of product and components configurations and long lead times of the sales process and of material procurement during project execution place additional planning challenges in comparison with a standardized high volume product business. The study focuses on improving the visibility on future customer orders and on reducing the procurement lead time of project material. Due to the nature of the market and the customers of the studied product line, incoming orders timing is very uncertain when viewed on a project by project basis. However, there is a specific dynamic when the sales pipeline is analyzed on aggregate: Tenders that end up converting into a customer order will do so sooner rather than later. Historical data and observations are used to develop and propose a probabilistic model that connects today's open tenders to the expected new business out of those tenders. The organization is able to use this model to estimate what the current activity of the sales force can produce in terms of new business. The expected benefit is that the organization can act proactively if there is an expected reduction in incoming business from a specific region or major customer; it can also make targeted efforts to increase sales activity towards that region or customer. To increase its competitiveness when bidding for new projects, the organization has embarked on an effort to reduce the overall project execution lead time. A significant portion of this lead time is waiting time for project specific material (which comprises the biggest part of the BOM in money terms). A supplier flexibility scheme is proposed, under which a material order is placed in two phases: first the desired delivery time and the component rough specification are specified, and later on the exact specs are given to the supplier. An optimization model that utilizes the above concept is developed and offers the organization an optimal way to plan the project material procurement, given a desired reduction in procurement lead time. The expected benefit is that there is a justified and optimal method to reduce procurement time without building excessive material stock; it also sheds light to the "constraints" (specific materials or suppliers) that need to be lifted for further lead time reduction.
Description
Thesis: M.B.A., Massachusetts Institute of Technology, Sloan School of Management, 2014. In conjunction with the Leaders for Global Operations Program at MIT. Thesis: S.M., Massachusetts Institute of Technology, Department of Mechanical Engineering, 2014. In conjunction with the Leaders for Global Operations Program at MIT. Cataloged from PDF version of thesis. Includes bibliographical references (page 77).
Date issued
2014Department
Leaders for Global Operations Program at MIT; Massachusetts Institute of Technology. Department of Mechanical Engineering; Sloan School of ManagementPublisher
Massachusetts Institute of Technology
Keywords
Sloan School of Management., Mechanical Engineering., Leaders for Global Operations Program.