Magnetic suspension and vibration control of flexible structures for non-contact processing
Author(s)
Weng, Ming-chih, 1969-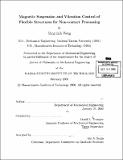
DownloadFull printable version (41.75Mb)
Other Contributors
Massachusetts Institute of Technology. Dept. of Mechanical Engineering.
Advisor
David L. Trumper.
Terms of use
Metadata
Show full item recordAbstract
This thesis presents the design, analysis, and experimental testing of systems for noncontact suspension and control of flexible structures. Our particular focus is on the use of such suspensions in manufacturing processes which can be facilitated by the ability to control workpiece motion without contact. This can be of significant utility in processes such as coating, painting, heat treating, and web handling. We develop a novel approach for the control of such non-contact suspensions through what we term sensor averaging and actuator averaging. The difficult stability and robustness problems imposed by the flexible dynamics of the workpiece can be overcome by taking a properly-weighted average of the outputs of a distributed array of N motion sensors (sensor averaging), and/or by applying a properly-weighted distributed array of M forces (actuator averaging) to the workpiece. The theory for these dual techniques is developed in detail in the thesis. These approaches are shown to be independent of the specific boundary conditions or the longitudinal dimensions of the workpiece. These approaches are thus generally applicable to a wide range of structural control problems. We present both analytical and numerical analyses of the structural dynamics for typical flexible workpieces such as strings, beams, membranes, and plates. The analyses include axial translation of the workpiece. We have experimentally demonstrated the utility of our theory by application in the successful magnetic suspension of a 3 m long, 6.35 mm diameter, 0.89 mm wall thickness steel tube with varying boundary conditions. This is a very challenging problem due to the extremely light damping of the modes (< 0.001 with free ends). The experiment uses a set of 8 sensors and 8 actuators to measure and control the motion of the tube in the two lateral degrees of freedom. We present the details of the developed electromagnetic actuators, position sensors, modeling of the structural dynamics, the relevant vibration control techniques, and develop the associated theory for choosing sensor and actuator locations. Our results experimentally confirm the value of our averaging techniques, and suggest the wide future application of these ideas in industrial processes which require non-contact handling of workpieces.
Description
Thesis (Ph.D.)--Massachusetts Institute of Technology, Dept. of Mechanical Engineering, 2000. Includes bibliographical references (p. 365-372).
Date issued
2000Department
Massachusetts Institute of Technology. Department of Mechanical EngineeringPublisher
Massachusetts Institute of Technology
Keywords
Mechanical Engineering.