Analysis, design, fabrication, and testing of a MEMS switch for power applications
Author(s)
Wong, Jo-Ey, 1968-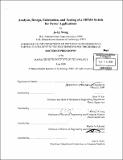
DownloadFull printable version (19.41Mb)
Alternative title
Analysis, design, fabrication, and testing of a micro-electro-mechanical systems switch for power applications
Other Contributors
Massachusetts Institute of Technology. Dept. of Mechanical Engineering.
Advisor
Nam P. Suh.
Terms of use
Metadata
Show full item recordAbstract
This thesis reports an electrostatic MEMS switch for power applications. The proposed switching system consists of an array of single-switch cells, and a parallel transistor-based protection circuit for arcless switching. Such a system design enables the switch development to focus on a normally-open single-pole-single-throw modular MEMS switch cell, which operates under coldswitching conditions. This leaves arcing-related issues, integration with of control/protection electronics, and more complicated switch configurations to higher system-level design. Achievable off-state standoff voltages of a switch cell are investigated through experimental measurements of electrical breakdown in micron-sized air gaps. Breakdown voltages exceeding 300 V are demonstrated across clean air gaps as small as 0.5 pm. Based on this, design theories and criteria are discussed for power switching applications. The goals for this application are low on-state resistance, low power consumption, high current capacity, and high off-state standoff voltage. Common geometries and actuation mechanisms for MEMS actuators are compared and the electrostatic actuation of a diaphragm switch cell is chosen because of its low actuation voltage and power, its compatibility with mainstream CMOS processing technologies, and its good thermal performance. Pneumatic actuation is used as a secondary tool for the validation of diaphragm integrity. The mechanical analysis of axisymmetric thin plates is studied and two diaphragm designs are proposed: a single-crystal silicon diaphragm of uniform thickness and a highly-tensile-stressed LPCVD nitride diaphragm. Switch prototypes employing vertically moving bulk-micromachined single-crystal silicon or LPCVD nitride diaphragms with highly-doped poly-silicon actuation electrodes and metal contacts are fabricated with an 8-mask IC-friendly process. Mechanical and electrical models of the MEMS switch cells are established analytically and are validated experimentally. Various characterization tests are executed to understand the behavior and the performance of the prototype switch cells. The switch cells can be switched electrostatically with 20 V or less, pneumatically with 1200 Pa, or through combined actuation. Metal-to-metal contact resistance measurements, performed using a four-point-probe technique, are normally below 50 M[Omega] and sometimes approach 15 M[Omega] while the current capacity in excess of 400 mA per switch cell in either current direction is demonstrated. An off-state resistance greater than 30 M[Omega] is achieved. The lowest un-damped resonant frequency of one of the diaphragm designs is calculated to be 19.8 kHz. The effects of the compressible air in the gap dominate the device switching speed as the squeeze-film characteristic time constant of this high radius-to-separation ratio gap is calculated to be 54 ms. Switching time are found to be on the order of 20-50 ms, which agrees with the squeeze-film characteristic time. Cyclic operation of the device is demonstrated without significant performance degradation. The switch cells exhibit essentially zero power consumption during stead state because of the nature of electrostatic actuation.
Description
Thesis (Ph.D.)--Massachusetts Institute of Technology, Dept. of Mechanical Engineering, 2000. Includes bibliographical references (p. 215-218).
Date issued
2000Department
Massachusetts Institute of Technology. Department of Mechanical EngineeringPublisher
Massachusetts Institute of Technology
Keywords
Mechanical Engineering.