Development of a microfabricated turbine-driven air bearing rig
Author(s)
Lin, Chuang-Chia, 1968-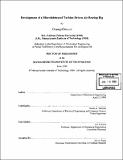
DownloadFull printable version (12.27Mb)
Advisor
Ain A. Sonin.
Terms of use
Metadata
Show full item recordAbstract
A team at MIT has been working to develop the technology for a micro gas turbine generator that is capable of converting chemical energy from fuel into electrical power. Such a MEMS device would represent a big leap in portable power source technology, providing ten times the power and energy density of batteries at competitive costs. The major fabrication challenge of realizing this miniature gas turbine generator is to demonstrate a baseline fabrication process capable of integrating the radial-inflow turbine rotor, bearings, and gas interconnects into a small package. The rotor is a 300 µm thick, 4 millimeter diameter disk supported by a nominally 10 µm wide air journal bearing. This structure, called the microbearing rig, is not only a vehicle for the development of a process methodology for fabrication of freely-rotating high aspect ratio devices, but it is also a vehicle for research into micro-fabricated gas bearings and rotordynamics. The process flow involves the use of 16 masks, 9 aligned deep reactive ion etching (ORIE) steps, aligned fusion bonding of a 5 wafer stack, and laser assisted etching. The device has been successfully fabricated, and the fabrication process will be presented, together with work in instrumentation, and packaging. In order to determine the necessary tolerances for the micro bearing fabrication and to provide performance parameters, calculations were performed based on a computational fluid dynamics and a semi-empirical model. The calculations are validated through comparison to the experimental measurements. Based on the model, improvements in thrust bearing design are implemented and fabricated. The increasing fabrication accuracy is reflected by constant improvement in device performance. So far, a stable speed of 296,000 rpm has been achieved. The approach taken to develop the fabrication process flow described can be applied in many areas to build devices with complicated micro-fluidic interconnects and devices with encapsulated free-moving parts. Data from the micro-thrust bearings are useful for miniature fluidic/hydraulic actuators. The micro-rotating machinery will open new opportunities for fabricating micro valves, pumps, micro-coolers, and micro-propulsion devices.
Description
Thesis (Ph.D.)--Massachusetts Institute of Technology, Dept. of Mechanical Engineering, 1999. Includes bibliographical references.
Date issued
1999Department
Massachusetts Institute of Technology. Department of Mechanical EngineeringPublisher
Massachusetts Institute of Technology
Keywords
Mechanical Engineering