Cost of complexity : mitigating transition complexity in mixed-model assembly lines
Author(s)
Addy, Robert.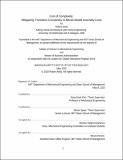
Download1191268336-MIT.pdf (1001.Kb)
Alternative title
Mitigating transition complexity in mixed-model assembly lines
Other Contributors
Sloan School of Management.
Massachusetts Institute of Technology. Department of Mechanical Engineering.
Leaders for Global Operations Program.
Advisor
Sang-Gook Kim and Steven Spear.
Terms of use
Metadata
Show full item recordAbstract
The Nissan Smyrna automotive assembly plant is a mixed-model production facility which currently produces six different vehicle models. This mixed-model assembly strategy enables the production level adjustment of different vehicles to match changing market demand, but it necessitates a trained workforce who are familiar with the different parts and processes required for each vehicle. Currently, the mixed-model production process is not batched; assembly line technicians might switch between assembling different vehicles several times every hour. When a switch or 'transition' occurs between different models, variations in the defect rate could occur as technicians must familiarize themselves with a different set of parts and processes. This thesis identifies this confusion as the consequence of 'transition' complexity, which results not only from variety but also familiarity; how quickly can a new situation be recognized, and how quickly can associates remember what to do and recover the skills needed to succeed. Recommendations follow to mitigate the impact of transition complexity on associate performance, thereby improving vehicle production quality. Transition complexity is an important factor in determining the performance of the assembly system (with respect to defect rates) and could supplement existing models of complexity measurement in assembly systems. Several mitigation measures at the assembly plant level are recommended to limit the impact of transition complexity on system performance. These measures include improvements to the offline kitting system to reduce errors such as reconfiguring the physical layout and implementing a visual error detection system. Additionally, we recommend altering the production scheduling system to ensure low volume models are produced at more regular intervals and with consistently low sequence gaps.
Description
Thesis: M.B.A., Massachusetts Institute of Technology, Sloan School of Management, in conjunction with the Leaders for Global Operations Program at MIT, May, 2020 Thesis: S.M., Massachusetts Institute of Technology, Department of Mechanical Engineering, in conjunction with the Leaders for Global Operations Program at MIT, May, 2020 Cataloged from the official PDF of thesis. Includes bibliographical references (page 72).
Date issued
2020Department
Sloan School of Management; Massachusetts Institute of Technology. Department of Mechanical Engineering; Leaders for Global Operations ProgramPublisher
Massachusetts Institute of Technology
Keywords
Sloan School of Management., Mechanical Engineering., Leaders for Global Operations Program.