Elastically Housed Kinematic Couplings for InterchangeableElectric Vehicle Batteries
Author(s)
Sams, Sarah A.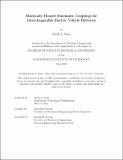
DownloadThesis PDF (20.21Mb)
Advisor
Slocum, Alexander
Terms of use
Metadata
Show full item recordAbstract
Commercial adoption of electric vehicle technologies has lagged due to immense charging downtime, but kinematic couplings have the potential to bridge this barrier by allowing for battery swaps and simultaneous operation and back-up battery charging. Designing parameters such as an elastic housing to damp the battery’s connection could overcome challenges with regard to manufacturing tolerance and operational loads. Accounting for proper preload and compliance for disturbance rejection is critical to maintain sufficient electrical contact while avoiding arcing. Kinematic couplings can provide enough contact area through Hertz line contact for a low resistance electrical contact, and Hertz stresses under loads are reasonable for conductive materials to bear without yield for long life cycles. This paper explored kinematic couplings as electrical conductors for electric vehicles by modifying a 2002 GEM E825. Kinematic coupling modifications decrease charging downtime by 98.33%. Elastic housings for ball-socket Kinematic couplings are predicted to increase the hertz contact area by 2684%, while decreasing the stress factor by 98.9% from a typical ball-groove kinematic coupling of the same size, allowing for larger vehicle batteries operated under higher forces and currents. Elastically housed kinematic couplings are a promising design pathway towards interchangeable electric vehicle batteries.
Date issued
2024-05Department
Massachusetts Institute of Technology. Department of Mechanical EngineeringPublisher
Massachusetts Institute of Technology