Feature-based investment cost estimation based on modular design of a continuous pharmaceutical manufacturing system
Author(s)
Collins, Donovan (Donovan Scott)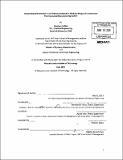
DownloadFull printable version (4.081Mb)
Other Contributors
Leaders for Global Operations Program.
Advisor
Bernhardt Trout and Charlie Fine.
Terms of use
Metadata
Show full item recordAbstract
Previous studies of continuous manufacturing processes have used equipment-factored cost estimation methods to predict savings in initial plant investment costs. In order to challenge and validate the existing methods of cost estimation, feature-based cost estimates were constructed based on a modular process design model. Synthesis of an existing chemical intermediate was selected as the model continuous process. A continuous process was designed that was a literal, step by step, translation of the batch process. Supporting design work included process flow diagrams and basic piping and instrumentation diagrams. Design parameters from the process model were combined with feature-based costs to develop a series of segmented cost estimates for the model continuous plant at several production scales. Based on this analysis, the continuous facility seems to be intrinsically less expensive only at a relatively high production scale. Additionally, the distribution of cost areas for the continuous facility differs significantly from the distribution previous assumed for batch plants. This finding suggests that current models may not be appropriate for generating cost estimates for continuous plants. These results should not have a significant negative impact on the value proposition for the continuous manufacturing platform. The continuous process designed for this project was not optimized. Therefore, this work reiterates that the switch to continuous must be accompanied with optimization and innovation in the underlying continuous chemistry.
Description
Thesis (M.B.A.)--Massachusetts Institute of Technology, Sloan School of Management; and, (S.M.)--Massachusetts Institute of Technology, Dept. of Chemical Engineering; in conjunction with the Leaders for Global Operations Program at MIT, June 2011. "June 2011." Cataloged from PDF version of thesis. Includes bibliographical references (p. 72-73).
Date issued
2011Department
Leaders for Global Operations Program at MIT; Massachusetts Institute of Technology. Department of Chemical Engineering; Sloan School of ManagementPublisher
Massachusetts Institute of Technology
Keywords
Sloan School of Management., Chemical Engineering., Leaders for Global Operations Program.