Passive and active approaches to sustained turbulent hydrodynamic drag reduction using superhydrophobic surfaces
Author(s)
Saranadhi, Dhananjai (Dhananjai V.)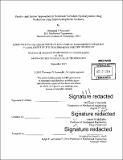
DownloadFull printable version (18.32Mb)
Other Contributors
Massachusetts Institute of Technology. Department of Mechanical Engineering.
Advisor
Gareth H. McKinley.
Terms of use
Metadata
Show full item recordAbstract
Superhydrophobic surfaces have been shown to trap a pocket of air (or a "plastron") in between the features of their rough texture when submerged in water. A partial slip condition is created at the interface between the water and the submerged body, allowing for a reduction in skin friction drag. I begin by identifying and fabricating several superhydrophobic surfaces, and testing their ability to reduce skin friction in turbulent flows using a bespoke Taylor-Couette apparatus. These superhydrophobic surfaces possess different surface topographies and chemistry, and exhibit different amount of drag reduction, leading to a deeper investigation of the role of surface chemistry and the roughness on the robustness of the plastron. The mean square slope as the driving roughness parameter in promoting plastron stability, and suggest methods by which it may be increased in order to optimize drag-reducing performance. The air plastron captured by a passive superhydrophobic surface represents one way of creating a slip boundary condition. An active approach can be used to augment slip at the boundary. With this approach, a submerged body is heated past its Leidenfrost temperature to form a thick, continuous film of steam between itself and the water. I continue to employ superhydrophobic surfaces, but now exploit their unique heat transfer properties (i.e. the insulation to heat transfer provided by the minimal contact area between the body and the surrounding water) to drastically reduce the Leidenfrost Temperature and Critical Heat Flux, and by extension the energy input required to create and sustain such a boiling film. In the active case, vapor film completely envelops the heated body and is thicker than a typical passive plastron, which allows for a significant increase in obtained drag reduction relative to a passive superhydrophobic surface. I design and fabricate a mechanism by which a Taylor-Couette rotor can be heated past its Leidenfrost point and continuously supplied with power to maintain a boiling film under rotation rates of 60 rad/s. The results show that skin friction can be reduced by over 90% relative to an unheated superhydrophobic surface at Re = 52,200, and I derive a boundary layer and slip theory to fit the data to a model that calculates a slip length of 1.04 ± 0.3 mm. This indicates that the boiling film has a thickness of 37 ± 9.5 [mu]m, which is consistent with literature.
Description
Thesis: S.M., Massachusetts Institute of Technology, Department of Mechanical Engineering, 2015. Cataloged from PDF version of thesis. Includes bibliographical references (pages 132-139).
Date issued
2015Department
Massachusetts Institute of Technology. Department of Mechanical EngineeringPublisher
Massachusetts Institute of Technology
Keywords
Mechanical Engineering.