Investing in quality : identifying the true value of advanced weld inspection technology
Author(s)
Buelsing, Michael T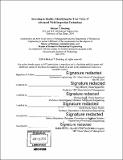
DownloadFull printable version (7.163Mb)
Alternative title
Identifying the true value of advanced weld inspection technology
Other Contributors
Leaders for Global Operations Program.
Advisor
Roy Welsch and Thomas Eagar.
Terms of use
Metadata
Show full item recordAbstract
The quality of Caterpillar's welds is becoming increasingly important as their equipment is made leaner with the goals of increased performance, lighter weight and lower unit cost. Due to the inherently variable nature of arc welding, non-destructive weld evaluation is critical to ensure that welding processes remain in control, and that defective parts are quarantined and repaired before being released downstream. The "conventional" ultrasonic weld inspection technology in use at present has several limitations: -- Areas within common joint configurations cannot be adequately inspected due to geometry constraints; -- Discontinuity evaluation requires subjective real-time human interpretation by highly trained operators; -- The data produced by the instrumentation is unconducive to recording for off-line analysis; -- Imprecise defect sizing leads to Type I and Type II inspection errors - the unnecessary rework of good parts, and the inappropriate release of non-complying parts. This project addressed these limitations of conventional ultrasonic weld inspection by identifying and evaluating alternative commercially available technologies and by initiating the internal development of specific proprietary technologies tailored to Caterpillar's needs. Through collaboration with Caterpillar's non-destructive evaluation (NDE) community, as well as outside vendors, a technology known as "phased array" was selected and validated in the laboratory and production environments. Although phased array was not new to Caterpillar, its adoption within the production facilities had previously been limited.
Description
Thesis: M.B.A., Massachusetts Institute of Technology, Sloan School of Management, 2016. In conjunction with the Leaders for Global Operations Program at MIT. Thesis: S.M. in Engineering Systems, Massachusetts Institute of Technology, Department of Mechanical Engineering, 2016. In conjunction with the Leaders for Global Operations Program at MIT. Cataloged from PDF version of thesis. Includes bibliographical references (page 51).
Date issued
2016Department
Leaders for Global Operations Program at MIT; Massachusetts Institute of Technology. Department of Mechanical Engineering; Sloan School of ManagementPublisher
Massachusetts Institute of Technology
Keywords
Sloan School of Management., Mechanical Engineering., Leaders for Global Operations Program.