Holistic modeling and evaluation of material recovery from materially-complex end-of-life vehicles
Author(s)
Ip Kiun Chong, Karine.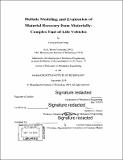
Download1139344941-MIT.pdf (63.88Mb)
Other Contributors
Massachusetts Institute of Technology. Department of Mechanical Engineering.
Advisor
Stephen C. Graves.
Terms of use
Metadata
Show full item recordAbstract
Material recovery is a key lever to promote a sustainable materials recycling system. By capturing materials from end-of-life products and substituting primary with secondary material production, society can reduce the depletion of natural resources and prevent the accumulation of valuable materials in landfills. Material recovery from materially-complex products, such as vehicles, is becoming more challenging as the material mixture becomes more heterogeneous with new trends in lightweight materials and product designs. The goals of this thesis are to develop a holistic modeling framework for material recovery for end-of-life vehicles (ELVs) and to illustrate the application of this framework to evaluate the recovery performance for current ELVs and future lightweight ELVs, using an existing material recovery infrastructure. The holistic framework encompasses an integrated series of material recovery models that span the recovery processes from grave to cradle: dismantling, hulk shredding, material separation, secondary metal production of steel and aluminum, and waste recovery from plastics. For each of these processes, we have developed an evaluative model using mass balance. The input into the recovery chain is the bill of materials of an ELV, including the assembly part hierarchies and assembly precedence constraints, as well as the material composition of all components and fasteners. The output from the recovery chain is an assessment of the value of the recovered scraps, based on the contribution of ferrous and aluminum scraps to secondary metal production, and of plastic residues to energy recovery. The intent of this holistic, grave-to-cradle framework is to allow one to rethink how the effectiveness of the recovery chain depends on the attributes of each of the end-of-life processes as well as on the vehicle product design. For the first phase of the recovery chain, we model the dismantling process as an optimization problem to decide what valuable parts to remove, given the parts' hierarchies and assembly precedence relationships, and the parts' values and dismantling costs. After removing these parts, we are left with the ELV hulk. For the second phase, we develop a shredding model for the comminution of the ELV hulk, i.e. the transformation of the hulk into non-liberated (fasteners and wires attached to parts' fragments) and liberated material particles of different sizes. For the third phase, we use a network flow model to model the sortation of the multi-material flow from the shredder through the network of sorting equipment, which performs separation based on material properties. Using this system of linear equations representing mass flow balance, we can solve for the material composition of the collected output scrap streams. From that, we can calculate the material quantity and quality losses due to inefficient separation. More importantly, this model is able to capture the metal contamination due to non-liberated particles ending up in the ferrous and aluminum scraps. For the fourth phase of the material recovery chain, we calculate the dilution losses incurred at secondary metal production for different scenarios of produced sink metal alloys. To tie together all losses from the material recovery chain, we propose the normalized contribution of scraps (NCS), an overall performance metric that improves upon the typical overall recovery rate (ORR) by accounting for the dilution losses. We illustrate the framework with a baseline ELV built from a family-car teardown data. In general, we observe the NCS to be significantly lower than the ORR (89%) for scenarios where the metal scraps are used to produce medium-quality alloys of the level of closed-loop recycling (NCS of 25% for 6061 Al alloy and rolled steel production), but not so much so when the metal scraps are down-cycled to low-quality alloys (NCS of 88 % for A380 Al alloy and steel bar production). We conduct two case studies to explore the effects of variations to the profile of the baseline ELV on its material recovery performance. In the first case study, we run Monte-Carlo simulations to model the uncertainty in the profile of the ELV hulks. Using data on the resale of used parts, we create a sample of 1000 different hulks by randomly generating the parts that are disassembled for resale. For this sample we observe that 300 kg of materials are removed from an ELV on average; the ORR varies from 86% to 91%, while the best-case scenario NCS varies from 60% to 91%. The second case study investigates the material recovery performance of an aluminum-intensive lightweight vehicle. For this vehicle, in comparison to the baseline vehicle, there is not only a higher concentration of aluminum, but also more ferrous fasteners in the aluminum body. Our analysis of this case suggests a decrease in recovery performance compared to that of the baseline ELV case. In comparison to the baseline vehicle, the lightweight vehicle has less ferrous, which results in a greater concentration of copper contaminant in ferrous scrap; thus, the ferrous scrap is of lower grade and requires more dilution. However, the increase in aluminum input is high enough to counter the increase in aluminum-ferrous particle contamination in the aluminum scrap. While the performance results depend on the model parameters representing the material recovery infrastructure, these case studies highlight the need for a holistic material recovery model to capture unintended dilution loss consequences due to changes in vehicle designs.
Description
Thesis: Ph. D., Massachusetts Institute of Technology, Department of Mechanical Engineering, 2019 Cataloged from PDF version of thesis. Includes bibliographical references (pages 244-252).
Date issued
2019Department
Massachusetts Institute of Technology. Department of Mechanical EngineeringPublisher
Massachusetts Institute of Technology
Keywords
Mechanical Engineering.