Macro scale physical model of nanoindentation on vertically aligned carbon nanotube forests
Author(s)
Ebeling, Geoffrey F. (Geoffrey Foster), 1981-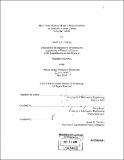
DownloadFull printable version (3.151Mb)
Other Contributors
Massachusetts Institute of Technology. Dept. of Mechanical Engineering.
Advisor
Mary Boyce.
Terms of use
Metadata
Show full item recordAbstract
Currently the process of nanoindentation is being explored as a reliable means of determining the mechanical properties of carbon nanotubes (CNTs) and the constituent tubes of vertically aligned carbon nanotube (VACNT) forests. Under indentation, each CNT can be modeled as a cantilevered beam subjected to deflection from the penetration of the indenter. The resistance to indentation is the result of the cumulative bending of the VACNTs. Using beam theory, the effective bending stiffness is determined by fitting the mechanical model to the indentation force-penetration curves. In order to validate the process of nanoindentation as a means of determining the elastic modulus of CNTs, a macro scale physical model was built using cylindrical rods of a known material and used to help explain some of the interactions of the tubes and indenter. Two models and two indenters were built to explore these effects and how they changed between models and indenters. The models demonstrated that for the indenter with a low face angle, the process was rather accurate with corresponding errors of 7% and 15%. When using a flatter indenter on both models, particularly the model with the higher areal density of tubes, demonstrated the inaccuracy of the process as a means for determining the elastic modulus of the material. Such a result was due to abnormal spikes in the data that were observable and attributed to tube interaction with the edge of the indenter. The process of indentation is reliable when the aberrations are minimal or are identifiable in the indentation force versus indentation depth curves and thus can be easily discounted. The process of scratching was also explored. For scratching the indenter is fixed at a certain indentation height and the tube forest (cont.) is then horizontally displaced and thus further deflects the tubes. The tubes enter three phases of contact, which subsequently affect the behavior of the scratching force versus distance curves. The macro scale model was used to validate the predicted behavior of CNTs. In general the scratching data supported the behavior of a three phase interaction between the tubes and indenter and the subsequent curves. For more accurate results and numerical comparisons, the forests need to be displaced using a constant speed linear stage and measured against distance.
Description
Thesis (S.B.)--Massachusetts Institute of Technology, Dept. of Mechanical Engineering, 2004. Includes bibliographical references (p. 55-56).
Date issued
2004Department
Massachusetts Institute of Technology. Department of Mechanical EngineeringPublisher
Massachusetts Institute of Technology
Keywords
Mechanical Engineering.