Thermal-hydraulic analysis of cross-shaped spiral fuel in high power density BWRs
Author(s)
Conboy, Thomas M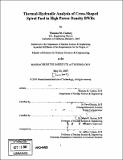
DownloadFull printable version (11.06Mb)
Alternative title
Thermal-hydraulic analysis of CSS fuel in high power density BWRs
Other Contributors
Massachusetts Institute of Technology. Dept. of Nuclear Science and Engineering.
Advisor
Pavel Hejzlar and Mujid S. Kazimi.
Terms of use
Metadata
Show full item recordAbstract
Preliminary analysis of the cross-shaped spiral (CSS) fuel assembly suggests great thermal-hydraulic upside. According to computational models, the increase in rod surface area, combined with an increase in coolant turbulence and inter-channel mixing will allow for a greater than 25% uprate in total core power, without loss of safety margin. Proper design of the rod dimensions can limit circumferential heat-flux to a peak-to-average ratio of 1.88. Non-uniformities in heat flux due to its unusual geometry seem to particularly ally CSS fuel to the BWR core, where limiting conditions are less likely to be locally influenced. Furthermore, the increase in cooling surface and reduction in central pin thickness is expected to drop fuel centerline temperature an estimated 2000C under nominal operating conditions, a reduction which rises to 3000C at 125% of nominal power conditions. In addition to these advantages, the absence of grid spacers within the CSS fuel assembly is expected to lower pressure losses, aiding natural convection and core stability. Spacers typically account for 25-30% of the total core pressure drop. Experimental measurements of hydraulic: losses for 1.5-meter-long model CSS rods in 4x4 arrays show a larger pressure drop at the same flow velocity than for bare cylindrical rods. However, this results in a CSS-bundle turbulent friction factor which is only 90% of the expected value given its hydraulic diameter. The effect of twist pitch on this pressure drop and friction factor is negligible in the range of twists examined. (cont.) Combined with the elimination of grid spacers, this results in a 40% reduction in core hydraulic loss from the reference case (neglecting entrance and exit plates). All told, the use of CSS rods should reduce total core pressure drop at nominal power by 9%, in spite of a reduction in core flow area. At 125% of nominal power, this becomes a 16% increase in pressure drop in comparison to the reference core at nominal power.
Description
Thesis (S.M.)--Massachusetts Institute of Technology, Dept. of Nuclear Science and Engineering, 2007. Includes bibliographical references (p. 199-201).
Date issued
2007Department
Massachusetts Institute of Technology. Department of Nuclear Science and EngineeringPublisher
Massachusetts Institute of Technology
Keywords
Nuclear Science and Engineering.