Contact-printed microelectromechanical systems
Author(s)
Murarka, Apoorva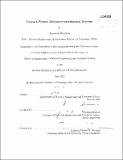
DownloadFull printable version (12.42Mb)
Other Contributors
Massachusetts Institute of Technology. Dept. of Electrical Engineering and Computer Science.
Advisor
Vladimir Bulović.
Terms of use
Metadata
Show full item recordAbstract
Microelectromechanical systems (MEMS) are ubiquitous. Scalable large-area arrays of MEMS on a variety of substrates, including flexible substrates, have many potential applications. Novel methods for additive fabrication of thin (125±15 nm thick) suspended gold membranes on a variety of rigid and flexible cavity-patterned substrates for MEMS applications are reported. The deflection of these membranes, suspended over cavities in a dielectric layer atop a conducting electrode, can be used to produce sounds or monitor pressure. The reported fabrication methods employ contact-printing, and avoid fabrication of MEMS diaphragms via wet or deep reactive-ion etching, which in turn removes the need for etch-stops and wafer bonding. Elevated temperature processing is also avoided to enable MEMS fabrication on flexible polymeric substrates. Thin films up to 12.5 mm2 in area are fabricated. The MEMS devices are electrically actuated and the resulting membrane deflection is characterized using optical interferometry. Preliminary sound production is demonstrated, and further applications of this technology are discussed.
Description
Thesis (M. Eng.)--Massachusetts Institute of Technology, Dept. of Electrical Engineering and Computer Science, 2012. Cataloged from PDF version of thesis. Includes bibliographical references (p. 105-107).
Date issued
2012Department
Massachusetts Institute of Technology. Department of Electrical Engineering and Computer SciencePublisher
Massachusetts Institute of Technology
Keywords
Electrical Engineering and Computer Science.