Fracture shearing of polycrystalline material simulations using the material point method
Author(s)
Raymond, Samuel J.; Jones, Bruce D.; Williams, John R.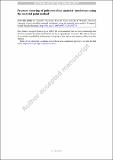
Download40571_2020_327_ReferencePDF.pdf (2.143Mb)
Open Access Policy
Open Access Policy
Creative Commons Attribution-Noncommercial-Share Alike
Terms of use
Metadata
Show full item recordAbstract
Abstract
In this work, we present a newly developed workflow to study the combined effect of shear and normal stresses upon a preexisting fracture plane. This workflow is used to study the behavior of both single grain and polycrystalline materials, with varying material properties. The surface roughness and aperture of preexisting fractures are highly dependent upon the dynamic stress behavior within rock formations. Due to shear slippage, or variation in normal stress, a preexisting fracture may become more or less conductive, leading to changes in effective porosity, where such changes are caused by purely elastic deformation, plastic deformation, material failure, or a combination thereof. The numerical modeling framework demonstrated herein is based upon the meshless material point method (MPM). In using MPM, the workflow can capture large deformations due to applied shear and normal stresses. Additionally, no special geometric treatment is required at the point of contact between fracture surfaces. Models involving purely elastic, single-grain materials, as well as more complex, plastic, polycrystalline bodies, are presented, highlighting the flexibility of the proposed approach.
Date issued
2020-03-12Department
Massachusetts Institute of Technology. Department of Civil and Environmental EngineeringPublisher
Springer International Publishing