A general constitutive model for dense, fine-particle suspensions validated in many geometries
Author(s)
Baumgarten, Aaron S; Kamrin, Ken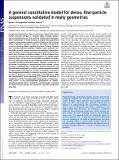
DownloadPublished version (1.973Mb)
Publisher Policy
Publisher Policy
Article is made available in accordance with the publisher's policy and may be subject to US copyright law. Please refer to the publisher's site for terms of use.
Terms of use
Metadata
Show full item recordAbstract
© 2019 National Academy of Sciences. All rights reserved. Fine-particle suspensions (such as cornstarch mixed with water) exhibit dramatic changes in viscosity when sheared, producing fascinating behaviors that captivate children and rheologists alike. Examination of these mixtures in simple flow geometries suggests intergranular repulsion and its influence on the frictional nature of granular contacts is central to this effect—for mixtures at rest or shearing slowly, repulsion prevents frictional contacts from forming between particles, whereas when sheared more forcefully, granular stresses overcome the repulsion allowing particles to interact frictionally and form microscopic structures that resist flow. Previous constitutive studies of these mixtures have focused on particular cases, typically limited to 2D, steady, simple shearing flows. In this work, we introduce a predictive and general, 3D continuum model for this material, using mixture theory to couple the fluid and particle phases. Playing a central role in the model, we introduce a microstructural state variable, whose evolution is deduced from small-scale physical arguments and checked with existing data. Our space- and time-dependent model is implemented numerically in a variety of unsteady, nonuniform flow configurations where it is shown to accurately capture a variety of key behaviors: 1) the continuous shear-thickening (CST) and discontinuous shear-thickening (DST) behavior observed in steady flows, 2) the time-dependent propagation of “shear jamming fronts,” 3) the time-dependent propagation of “impact-activated jamming fronts,” and 4) the non-Newtonian, “running on oobleck” effect, wherein fast locomotors stay afloat while slow ones sink.
Date issued
2019Department
Massachusetts Institute of Technology. Department of Aeronautics and Astronautics; Massachusetts Institute of Technology. Department of Mechanical EngineeringJournal
Proceedings of the National Academy of Sciences of the United States of America
Publisher
Proceedings of the National Academy of Sciences