Surface skeleton generation based on 360-degree profile scan
Author(s)
Chen, Lujie; Sass, Lawrence; Noel, Vernelle; Sung, Woongki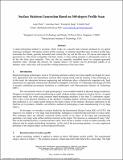
DownloadSass_Surface skeleton.pdf (757.6Kb)
PUBLISHER_POLICY
Publisher Policy
Article is made available in accordance with the publisher's policy and may be subject to US copyright law. Please refer to the publisher's site for terms of use.
Terms of use
Metadata
Show full item recordAbstract
A rapid prototyping method is invented, which works on a specific data structure produced by an optical metrology technique: 360-degree surface profile scanning. A computer algorithm takes an object profile data, restructure the format, generate horizontal and vertical ribs, lay out the ribs on a 2D canvas and output the geometries to a file format compatible with laser cutters. A laser cutting machine is subsequently used to cut all the ribs from sheet materials. Then, the ribs are manually assembled based on computer-generated assembly codes. Through this process, the original object’s 3D surface can be prototyped rapidly at an arbitrary scale, which may well exceed the working dimension of the laser cutter.
Date issued
2013-05Department
Massachusetts Institute of Technology. Department of ArchitectureJournal
Proceedings of SPIE--the International Society for Optical Engineering
Publisher
SPIE
Citation
Chen, Lujie, Lawrence Sass, Woong Ki Sung, and Vernelle Noel. “Surface Skeleton Generation Based on 360-Degree Profile Scan.” Edited by Luca Pezzati and Piotr Targowski. Optics for Arts, Architecture, and Archaeology IV (May 30, 2013). © Society of Photo-Optical Instrumentation Engineers (SPIE)
Version: Final published version
ISSN
0277-786X